Pneumatic Conveying Systems
Design and manufacturing of pneumatic conveying systems applied to multiple industries
Pneumatic Conveying Systems
Design and manufacturing of pneumatic conveying systems applied to multiple industries
Pneumatic Conveying Systems
Design and manufacturing of pneumatic conveying systems applied to multiple industries
Pneumatic Conveying Systems
Design and manufacturing of pneumatic conveying systems applied to multiple industries
Pneumatic Conveying Systems
Design and manufacturing of pneumatic conveying systems applied to multiple industries
Pneumatic Conveying Systems
Design and manufacturing of pneumatic conveying systems applied to multiple industries
Pneumatic Conveying Systems
Design and manufacturing of pneumatic conveying systems applied to multiple industries
Pneumatic Conveying Systems
Design and manufacturing of pneumatic conveying systems applied to multiple industries
Pneumatic Conveying Systems
Design and manufacturing of pneumatic conveying systems applied to multiple industries
Pneumatic Conveying Systems
Design and manufacturing of pneumatic conveying systems applied to multiple industries
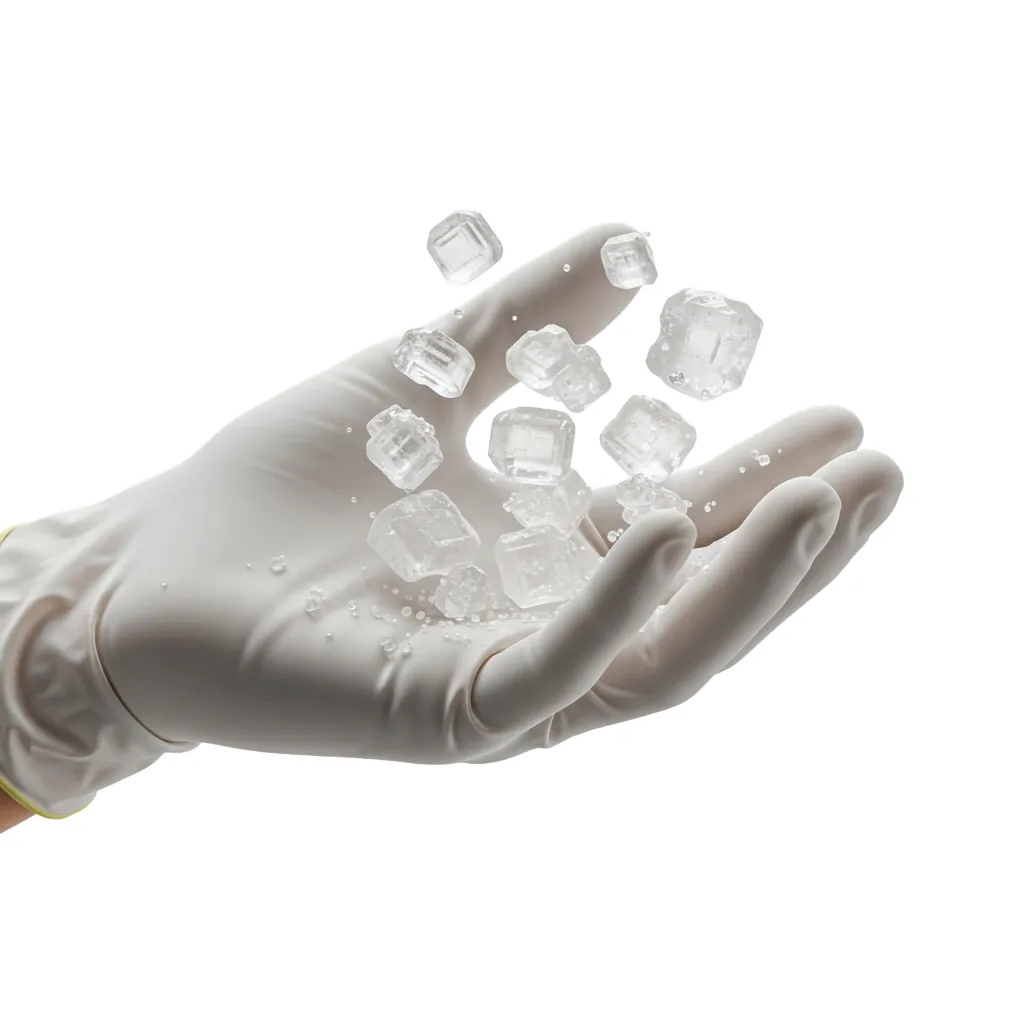
Advanced Industrial
Specialists in Advanced Industrial Pneumatic Conveying Systems
de Transporte
Neumático Industrial
Since its founding, OGA has stood out for its expertise in the design and manufacturing of advanced industrial pneumatic conveying systems.with a primary focus on Dilute Phase and Dense Phase. Our systems not only automate processes from precise feeding to complex material handling systems with multiple origin and/or destination points, but also integrate automatic weight control, process management, batching, inventory control, bulk handling, big bag handling, and more.
Soluciones Integrales de Transporte Neumático
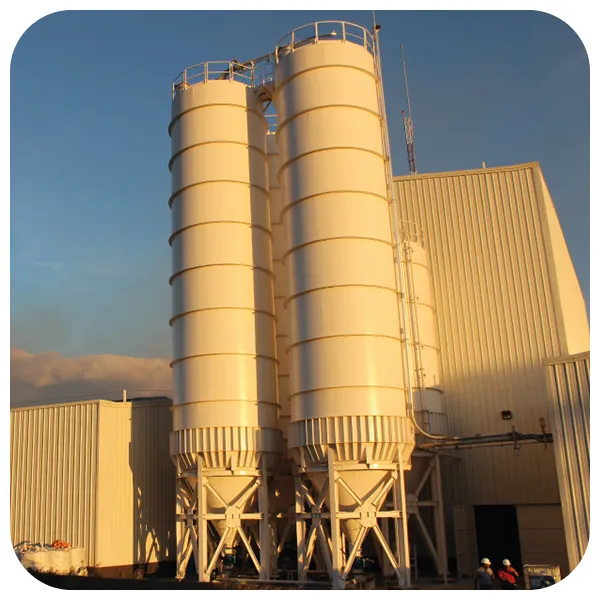
- Pneumatic Conveying Systems: Design and manufacturing of advanced material conveying solutions.
- Industrial Automation: Enhancing efficiency and productivity in industrial processes.
- Industrial Suction Equipment: Specialized tools for the safe handling of loads.
- Storage Silos: Efficient and secure storage solutions.
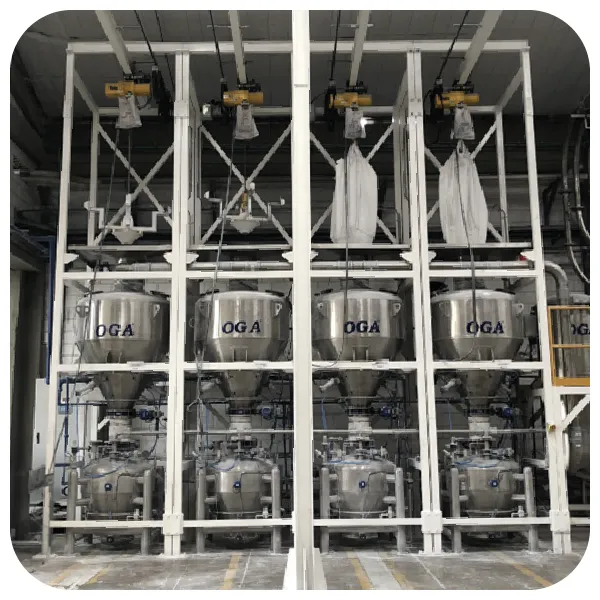
- Magnetic Separation: Advanced technology for material separation.
- Raw Material Classification: Innovative systems for the precise classification of raw materials.
- Bag Unloading: Specialized equipment for the fast and efficient unloading of products.
- Industrial Vacuum or Dust Collector: High-performance industrial cleaning solutions.
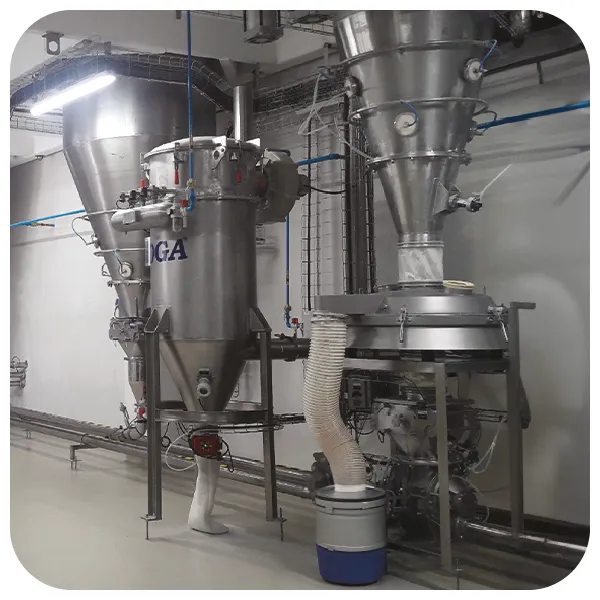
- Dust Extractor: Efficient equipment for dust collection in industrial environments.
- Sieve and Pneumatic Conveyor: Advanced technology for bulk material handling and processing.
- Supervision and Control Software: Specialized tools for efficient process supervision and control.
- Computer-Aided Design (CAD): Utilization of advanced CAD software for the design of customized solutions.
In-Line Gravimetric Dosing Systems
OGA has developed solid handling systems that, using gravimetric principles, determine the performance of continuous production processes. Based on pre-programmed process parameters, these systems enable the continuous addition and mixing of minor components, which are also weight-controlled for precise dosing. These systems create a control loop that automatically regulates dosing according to fluctuations in the production process's consumption.
Design and Manufacturing of Industrial Plants
Gathering decades of experience in the industrial sector and the multiple implemented production processes, OGA, through its equipment, integrates industrial process developments focused on process optimization, time efficiency, performance, traceability, and overall effectiveness. The starting point for all our solutions is an in-depth analysis of process requirements, identifying key impact areas to be incorporated into the designed process.
Systems with Supervision Software
OGA systems feature a control system that can be integrated into the plant's general software, allowing automatic interaction with the entire facility. This process enables variable visualization, process traceability, hierarchical control levels, automated maintenance tasks, remote supervision via the internet, weight reporting, and seamless integration with other process equipment.
– Weight measurement in silos for determining raw material inventory, serving as a confirmation model for received products and ensuring traceability of material delivered to production lines.
– Inclusion of recipes via software, where predefined addition weights per raw material and discharge timings into the mixing process are determined. Once the system enters automatic operation, the OGA system performs the dosing of each component, generating a report that includes (Target Weight, Delivered Weight, Shift Operator, Dosing Time, Manufactured Batch, among other control variables such as temperature, pressure, etc.).
– Generation of reports on plant consumption and performance, with information stored in databases for future consultation and traceability (Measurements, Storage, Comparisons, Mixing Components, Process Batches, Operating Times for Each Production Line).
- Pneumatic Conveying of Highly Abrasive Products
- Manejo de Materiales Bajo Normatividad ATEX
- Storage Silo Feeding via Pneumatic Conveying
- Storage Silos
- Product Feeding to Process
- Sieving and Classification of Solids
- Conveying of Products Susceptible to Demixing
- Material Handling Systems with ASME-Certified Equipment
- Supply of Bulk Tilting Platforms
- Silo Weighing System
- Inventory Control
- Pneumatic Conveying of Blended Product with CV Commitment
- Big Bag Handling
- Solids Dosing to Mixers