Pneumatic Conveying Systems
Design and manufacturing of pneumatic conveying systems applied to multiple industries
Pneumatic Conveying Systems
Design and manufacturing of pneumatic conveying systems applied to multiple industries
Pneumatic Conveying Systems
Design and manufacturing of pneumatic conveying systems applied to multiple industries
Pneumatic Conveying Systems
Design and manufacturing of pneumatic conveying systems applied to multiple industries
Pneumatic Conveying Systems
Design and manufacturing of pneumatic conveying systems applied to multiple industries
Pneumatic Conveying Systems
Design and manufacturing of pneumatic conveying systems applied to multiple industries
Pneumatic Conveying Systems
Design and manufacturing of pneumatic conveying systems applied to multiple industries
Pneumatic Conveying Systems
Design and manufacturing of pneumatic conveying systems applied to multiple industries
Pneumatic Conveying Systems
Design and manufacturing of pneumatic conveying systems applied to multiple industries
Pneumatic Conveying Systems
Design and manufacturing of pneumatic conveying systems applied to multiple industries
Confectionery and Chocolate Industry
Pneumatic Conveying Systems
OGA SISTEMVAC’s pneumatic transport systems in the confectionery and chocolate industry stand out for their efficiency and safety. Specializing in handling raw materials such as flour, chocolate, sugar, citric acid, colorants, sweeteners, stabilizers, sweeteners, cocoa, panela, sorbitol, and others, our systems are designed to adapt to the specific needs of each producer. The applications executed in the confectionery and chocolate industry reaffirm our expertise in the comprehensive development of pneumatic transport systems. These systems allow for efficient handling of raw materials such as flour, chocolate, sugar, citric acid, colorants, sweeteners, stabilizers, sweeteners, cocoa, panela, sorbitol, and others, adapting to each company’s specifications.
Good Manufacturing Practices (GMP) in Pneumatic Transport: OGA systems are designed and manufactured under the Good Manufacturing Practices (GMP) model, ensuring safe, cost-effective, and successful implementations. Each development includes essential concepts such as protection against cross-contamination, elimination of accumulation points, ease of cleaning, traceability, and demanding finishes, aligned with industrial demands.
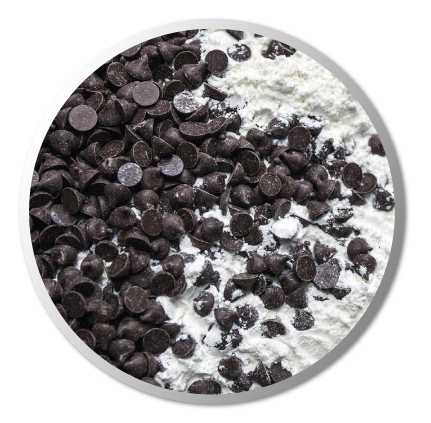
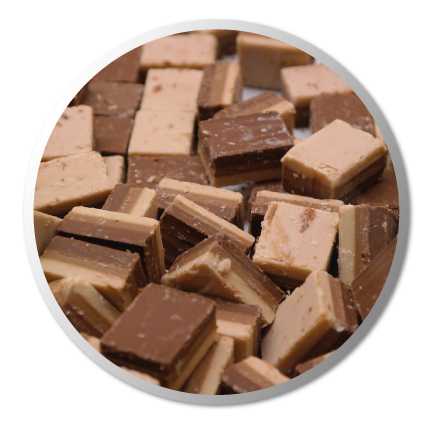
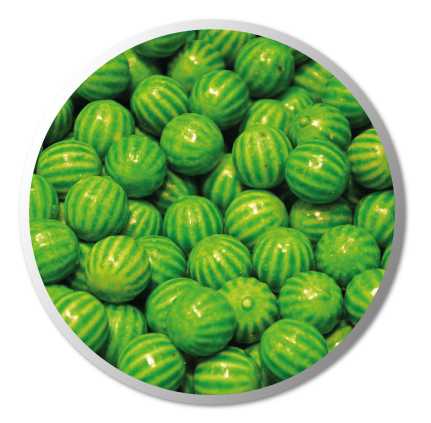
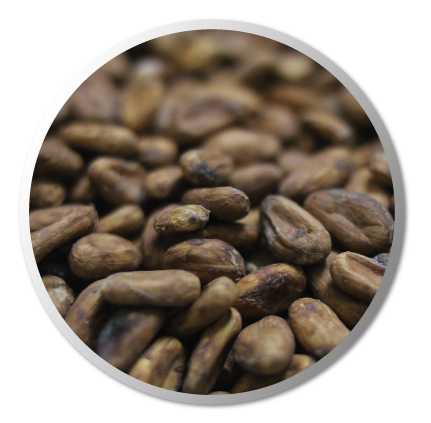
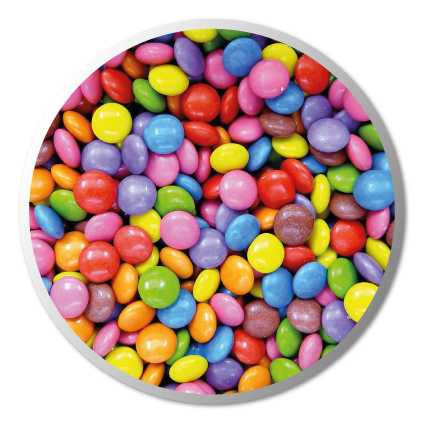
Pollution Control in the Confectionery and Chocolate Industry:
In the confectionery and chocolate industry, controlling, preventing, and securing raw materials is crucial. OGA pneumatic transport systems ensure rigorous pollution control, protecting the product from external contaminants and complying with international regulations.
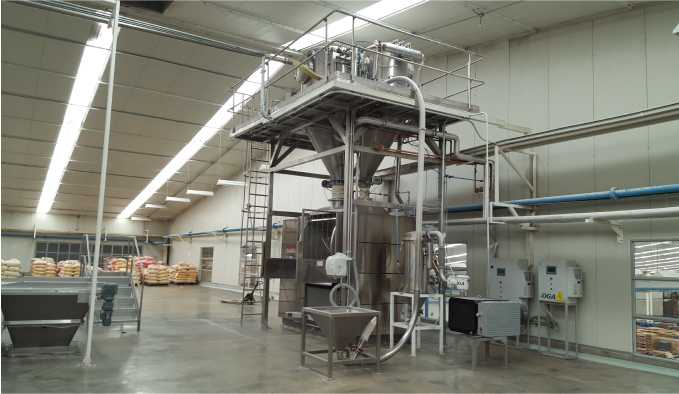
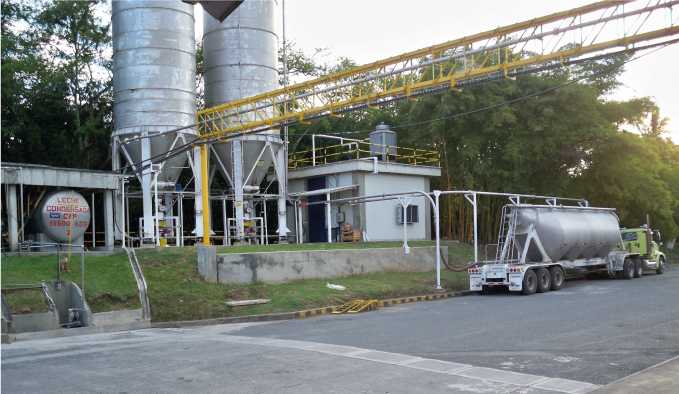
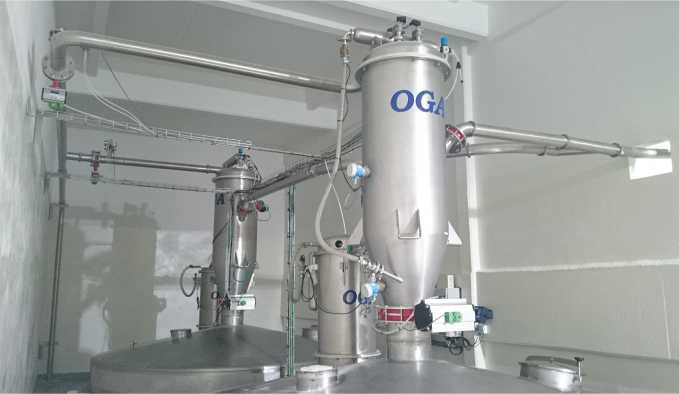
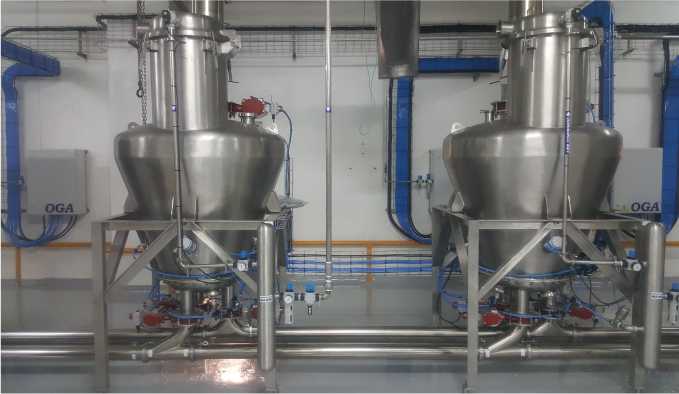
Chewing Gum
Systems Our systems for the manufacture of chewing gum optimize each production phase, minimizing coating breakage and degradation, preserving the product’s geometry, and preventing cross-contamination. OGA ensures efficient transport in mixers, pre-extruders, extruders, and during packaging.
- Minimal breakage of chewing gum coating
- No coating degradation of chewing gum
- Preservation of the product’s characteristic geometry
- No impact on the gum fillings
- No cross-contamination between chewing gum of different colors
- No segregation of powdered gum.
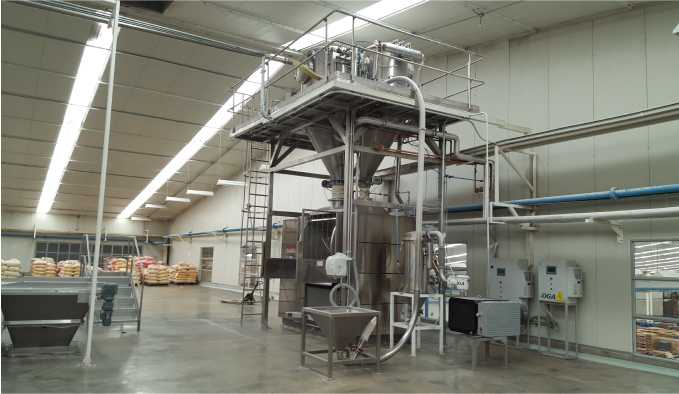
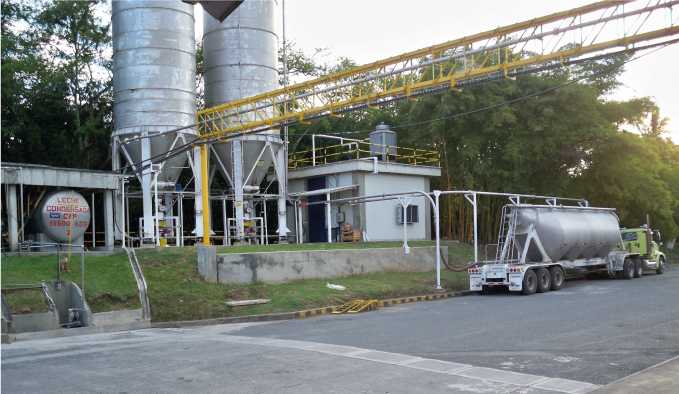
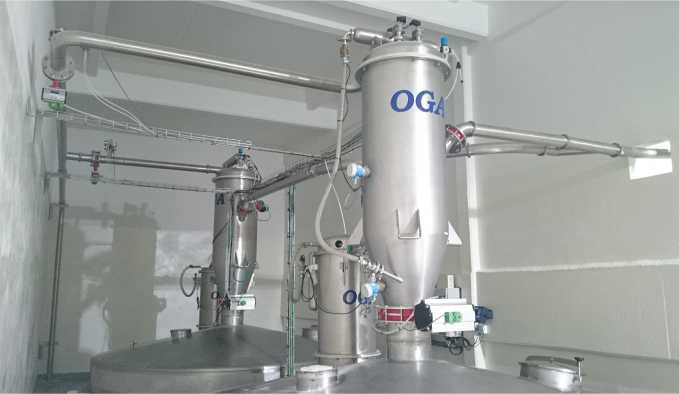
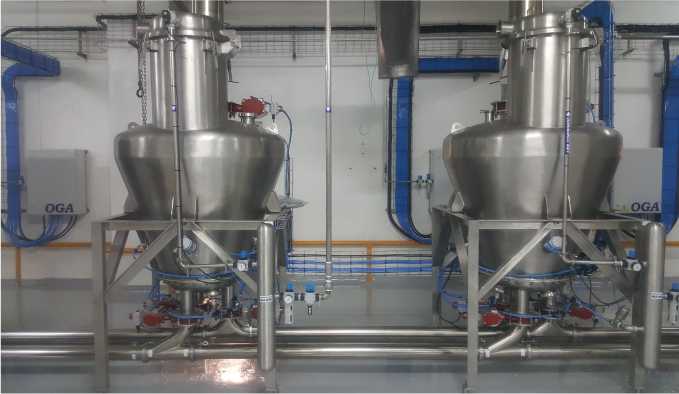
Systems Our systems for the manufacture of chewing gum optimize each production phase, minimizing coating breakage and degradation, preserving the product’s geometry, and preventing cross-contamination. OGA ensures efficient transport in mixers, pre-extruders, extruders, and during packaging.
Chewing Gum
- Minimal breakage of chewing gum coating
- No coating degradation of chewing gum
- Preservation of the product’s characteristic geometry
- No impact on the gum fillings
- No cross-contamination between chewing gum of different colors
- No segregation of powdered gum.
In addition to a broad portfolio of references, OGA pneumatic transport systems can move the product from its point of origin throughout the production plant, combining vertical and horizontal paths with a single pipe equipped with long-radius bends. This allows for multiple route derivations, serving different destination points and complying with HACCP, GMP, and FSSC 22000 regulations.
Additionally, complementary processes derived from the main systems include:
- Silo Weighing System
- Inventory Control
- Delicate Product Conveying
- Handling of Big Bags or Bulk Bags
- Solid Dosage
- Handling of Highly Abrasive Products
- Material Handling Systems Under ATEX Regulations (Upon customer request)
- Storage Silo Feeding via Pneumatic Conveying
- Storage Silos
- Product Feeding to Process
- Sieving, Solid Classification, and Product Cleaning
- Conveying of Products Susceptible to Demixing
- Material Handling Systems with ASME Equipment (Upon customer request)
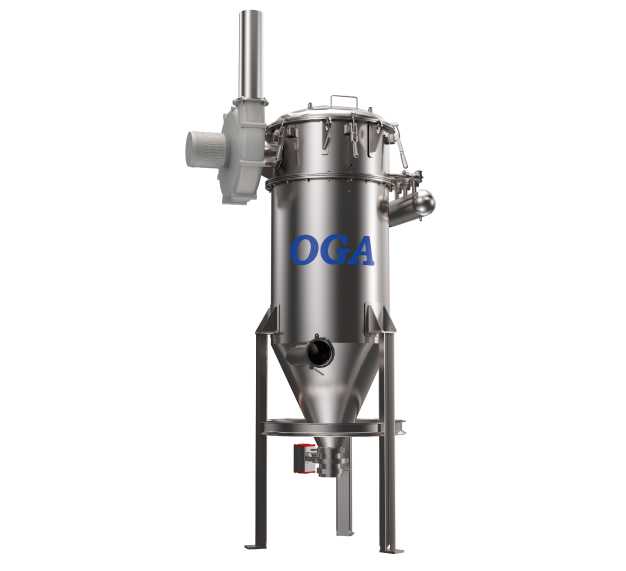
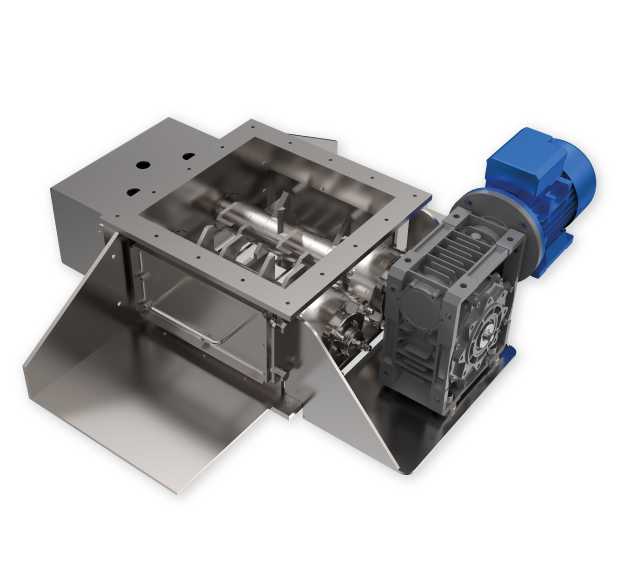
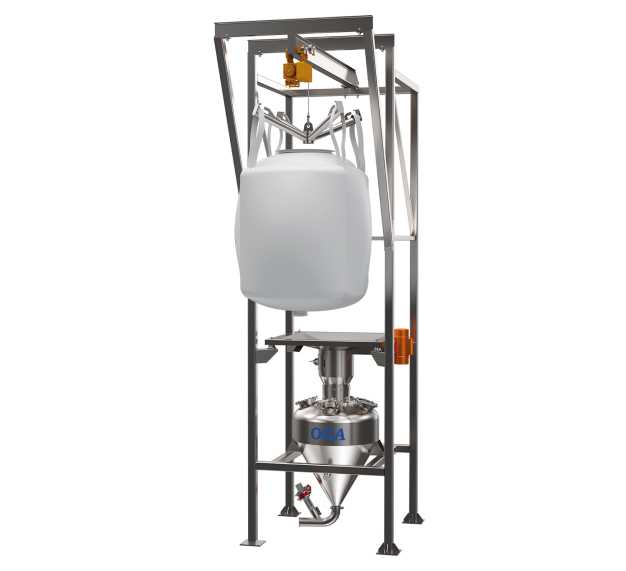
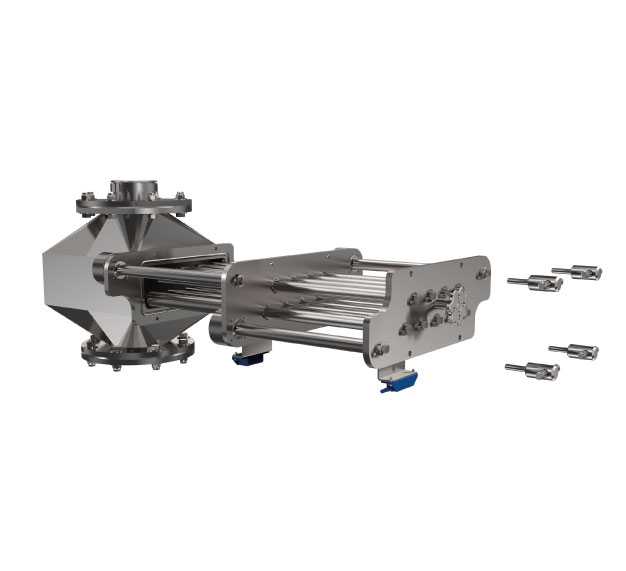
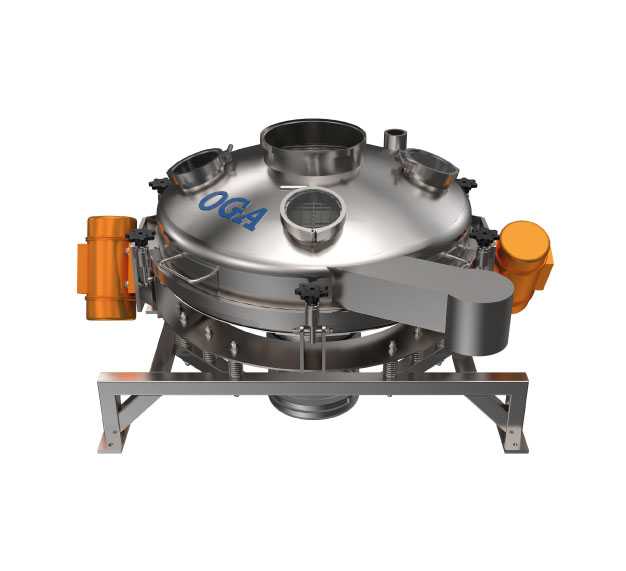
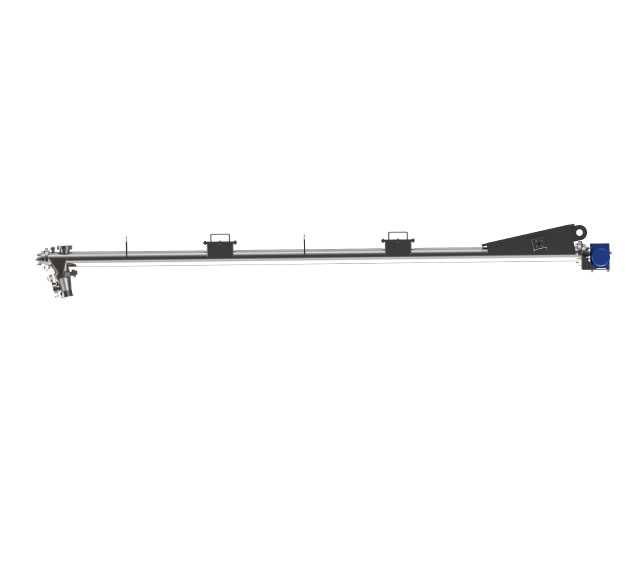
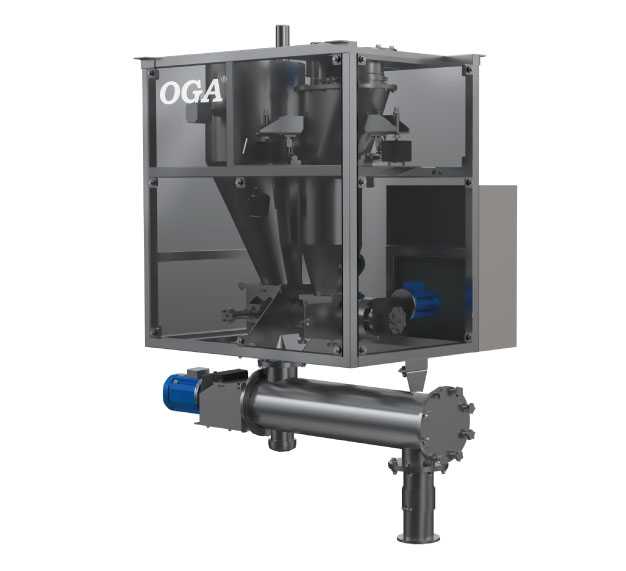
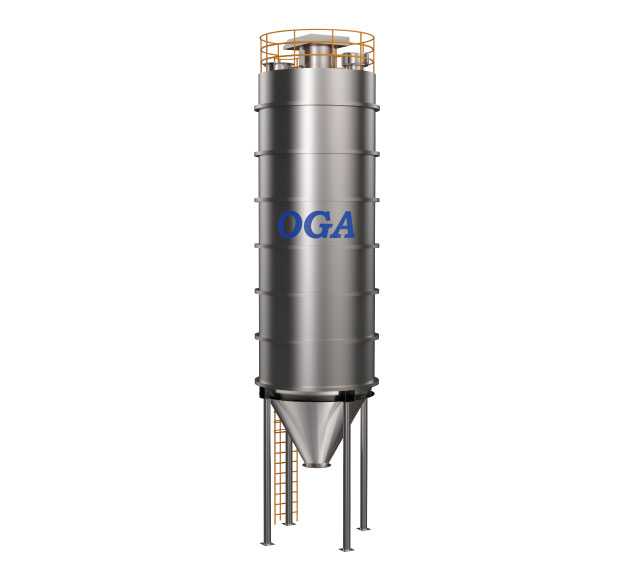
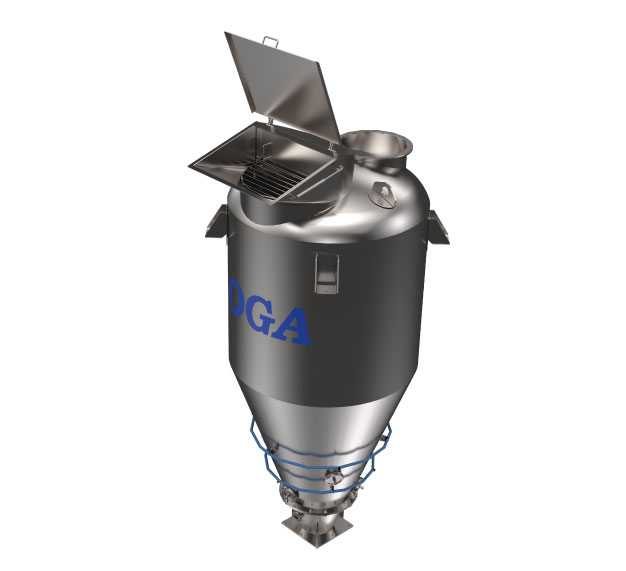

Additionally, complementary processes derived from the main systems include:
- Silo Weighing System
- Inventory Control
- Delicate Product Conveying
- Handling of Big Bags or Bulk Bags
- Solid Dosage
- Handling of Highly Abrasive Products
- Storage Silos
- Product Feeding to Process
- Sieving, Solid Classification, and Product Cleaning
- Conveying of Products Susceptible to Demixing
- Material Handling Systems with ASME Equipment (Upon customer request)
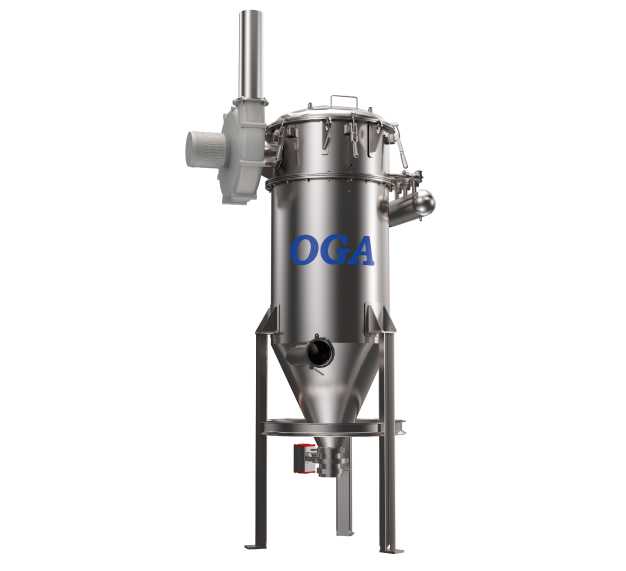
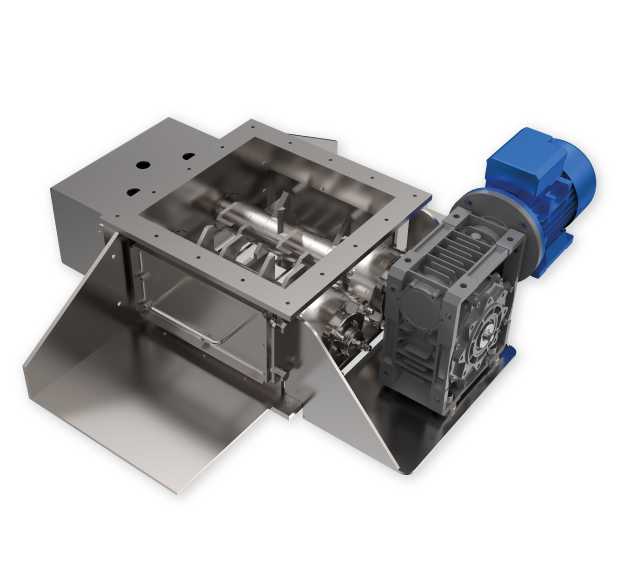
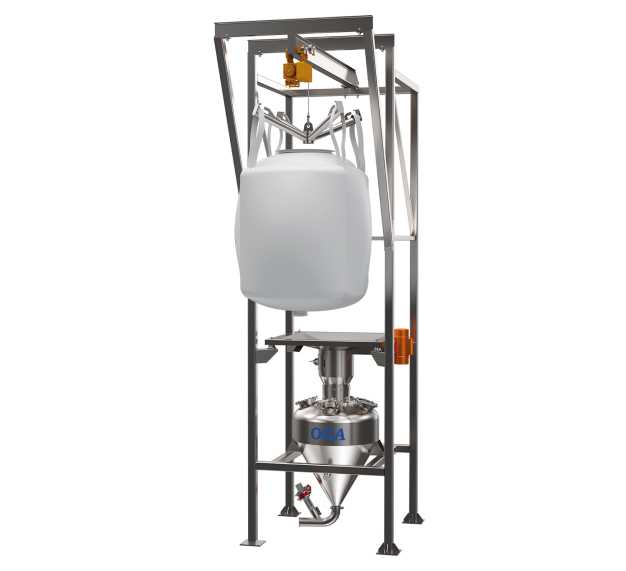
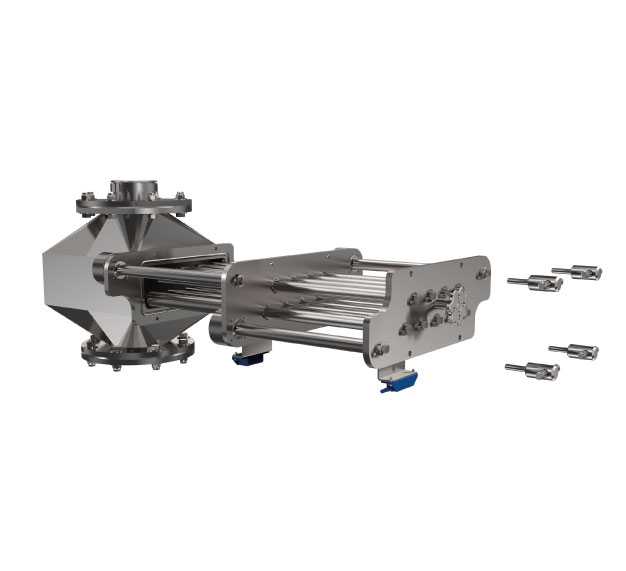
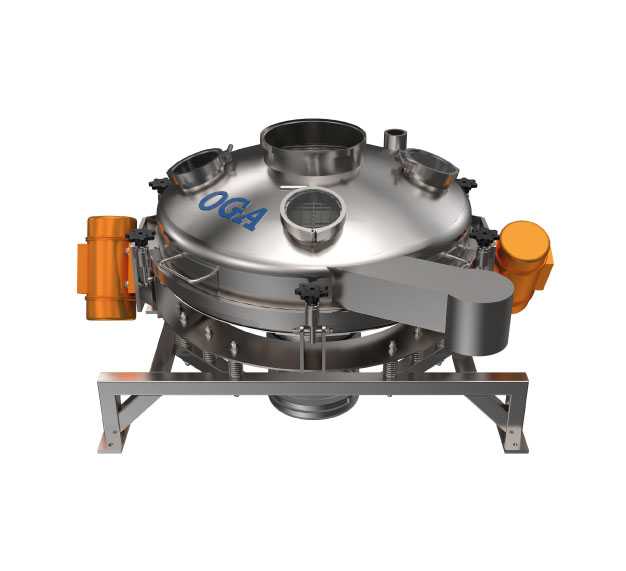
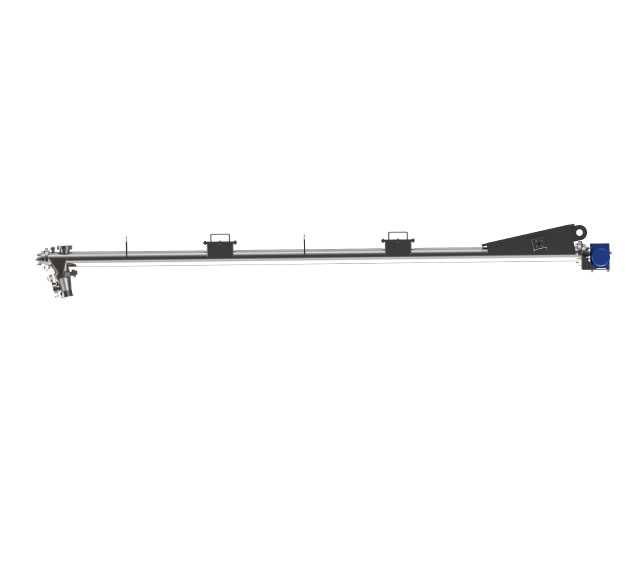
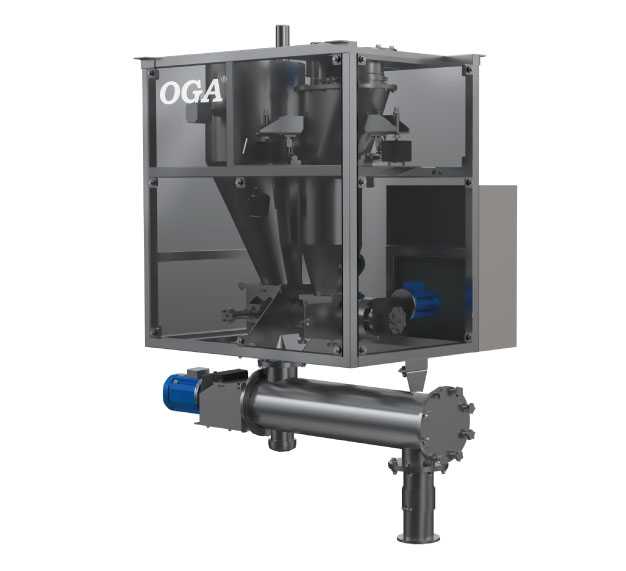
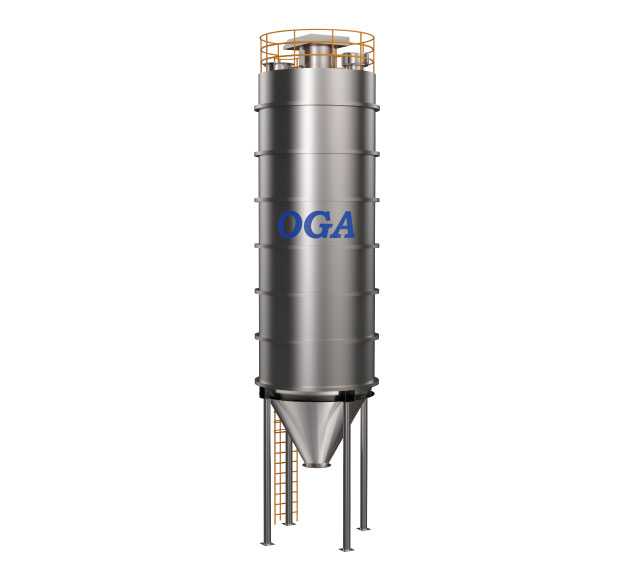
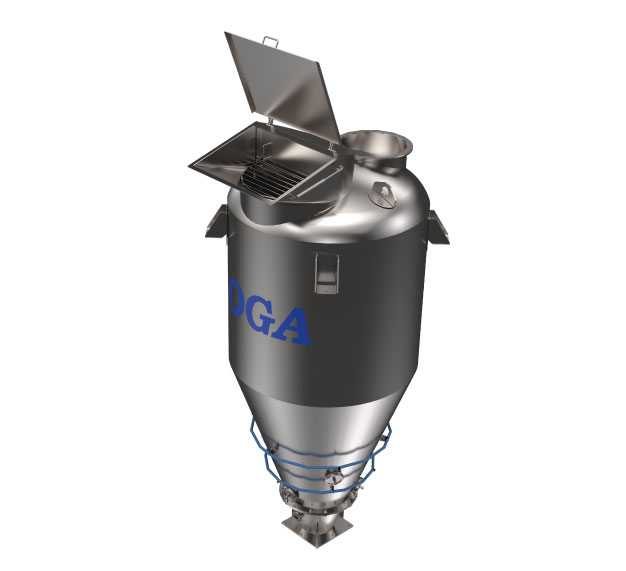

- Material Handling Systems Under ATEX Regulations (Upon customer request)
- Storage Silo Feeding via Pneumatic Conveying