Specialists in Pneumatic Conveying for the PVC Plastics Industry
Pneumatic Conveying
With over 26 years of global experience, we have become an iconic company in providing comprehensive pneumatic conveying solutions for the PVC plastics industry. Our continuous process innovation within the Industry 4.0 framework has led to numerous advanced applications.
Years of Global Operations
Our expertise spans the PVC plastics industry across Central America, the Caribbean, South America, Europe, and the Middle East.
Installed Projects
We have successfully installed over 3,000 projects in leading plastic manufacturing companies worldwide.



Specialists in Pneumatic Conveying for the PVC Plastics Industry
Pneumatic Conveying
With over 26 years of global experience, we have become an iconic company in providing comprehensive pneumatic conveying solutions for the PVC plastics industry. Our continuous process innovation within the Industry 4.0 framework has led to numerous advanced applications.



Years of Global Operations
Our expertise spans the PVC plastics industry across Central America, the Caribbean, South America, Europe, and the Middle East.
Installed Projects
We have successfully installed over 3,000 projects in leading plastic manufacturing companies worldwide.

Mode of Intervention
In the PVC plastics and piping industry, raw materials are typically received in bags, big bags, or in bulk. From this stage, OGA intervenes in material handling through loading and unloading systems tailored to each company. There are two modes of intervention: gradual and direct to the process.
The first mode involves unloading and transporting raw materials to storage silos, while the second entails the direct transfer of raw materials to specific process stages, such as mixing towers, extruders, injectors, blow molders, co-extruders, or other equipment.

Complementary Systems
- Bulk Unloading Systems from Containers to Silos
- Storage Silos for Powder or Granular Products
- Continuous Gravimetric Mixing Systems in Permanent Production Lines
- Production Process Control via SCADA Software
- Bulk Unloading Systems from Pressurizable Hopper Cars
- Raw Material Silo Weighing Systems
- Sieving Systems and Granulometric Selection of Raw Materials and Final Products
- Design of production plants based on solids handling and good manufacturing practices.
- Discharge systems from rail hoppers to silos.
- Conveying systems to daily silos within production plants.
- Automatic feeding of production processes from daily silos.
- Big bag unloading systems and conveying to storage silos.
- Gravimetric batching system for mixers.
- Control and reporting of raw material consumption by line and/or production process.

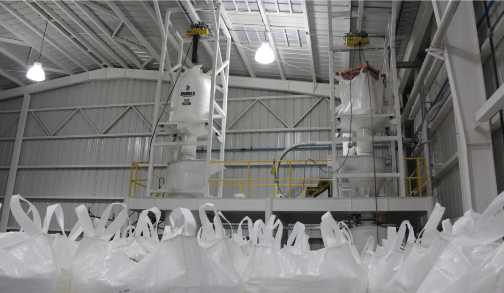
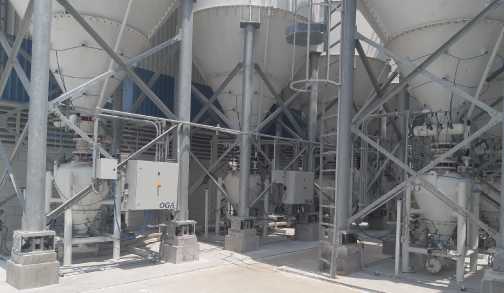
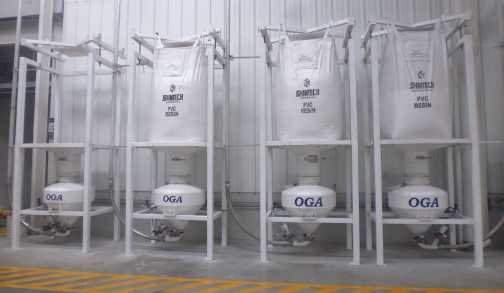
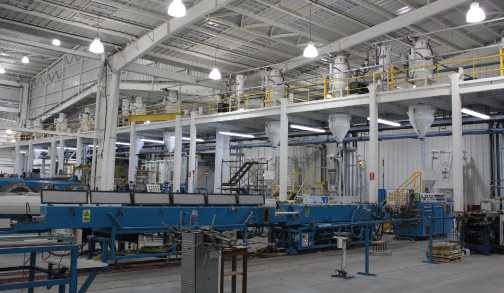
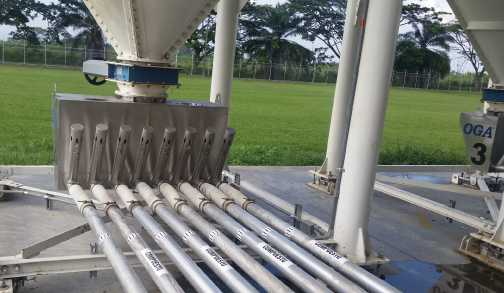
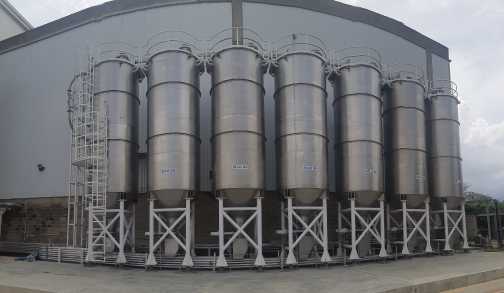
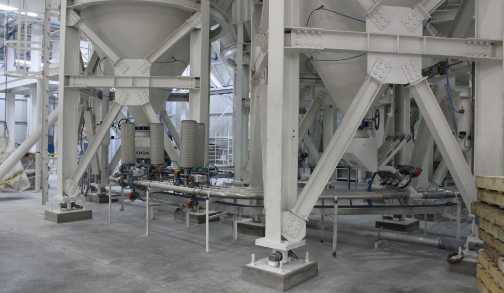
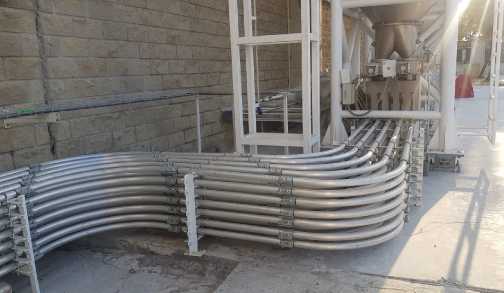
We specialize in the design and construction of PVC pipe production plants. Our developments cover everything from raw material reception to the final delivery of the compound to extrusion and injection machines.
OGA systems feature SCADA control models, enabling real-time operation monitoring both locally and remotely. This technology is adaptable to each industry's requirements for supervision, inspection, control, and data management.
To meet the specific needs of the industry, we offer systems for in-line carbonate addition, as well as the addition of pulverized materials or powdered colorants directly onto the machine. These solutions enhance the product’s physical properties while reducing production costs.

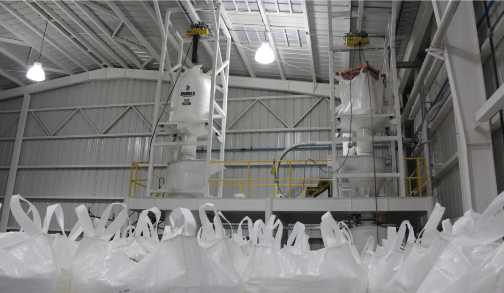
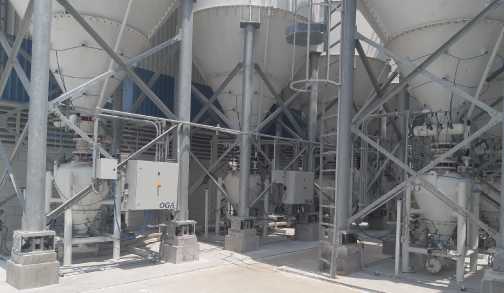
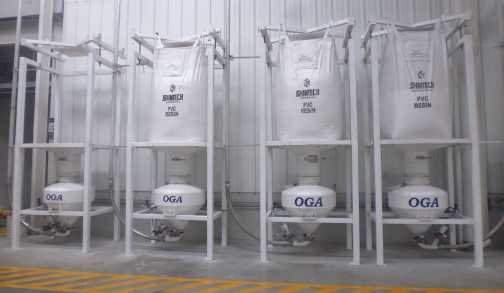
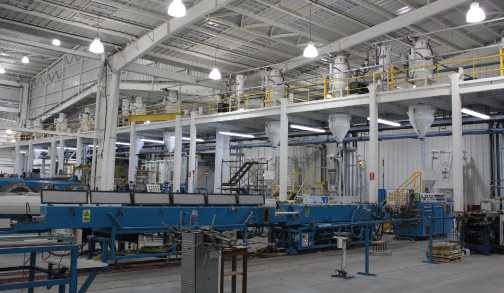
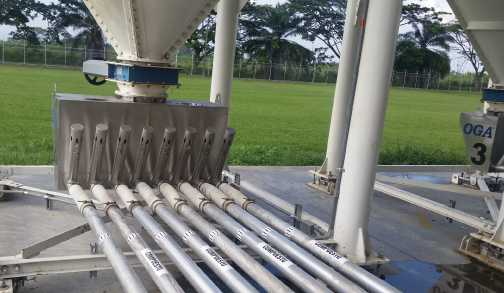
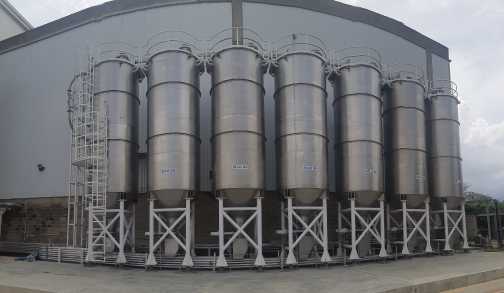
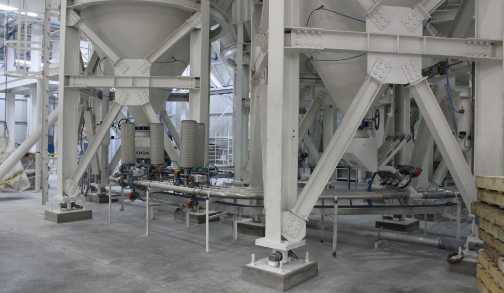
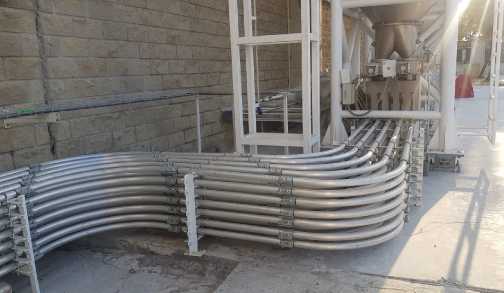
We specialize in the design and construction of PVC pipe production plants. Our developments cover everything from raw material reception to the final delivery of the compound to extrusion and injection machines.
OGA systems feature SCADA control models, enabling real-time operation monitoring both locally and remotely. This technology is adaptable to each industry's requirements for supervision, inspection, control, and data management.
To meet the specific needs of the industry, we offer systems for in-line carbonate addition, as well as the addition of pulverized materials or powdered colorants directly onto the machine. These solutions enhance the product’s physical properties while reducing production costs.

Types of Installed Systems

1. Raw Material Silo Feeding
– Reception of raw material in rail hoppers.
– Reception of raw material in hopper trucks.
– Reception of raw material in containers.
– Reception of raw material in conventional truck bodies.
– Reception of raw material from big bags.
– Reception of raw material from 50 kg and 25 kg sacks.
2. Raw Material Storage Silos
3. Inventory Control in Raw Material Silos by Weight
4. Transport of Solid and Liquid Raw Materials to the Mixing Tower
5. Bulk Component Dosing to Turbo Mixers
6. Automatic Dosing of Microcomponents by Recipe to Turbo Mixer
7. Double Batch Handling to Cooler
8. Production Control of Blended Materials via Gravimetric System
9. Screening of Manufactured Compound
10. Transport of Compound to Destination and Test Silos
11. Compound Silos
12. Gravimetric Inventory Control of Compound Silos
13. Automatic PVC Compound Transport System to Extrusion Lines
14. Automatic PVC Compound, Purge, or Pulverized Material Transport System to Extrusion Line
15. Direct Addition System for Calcium Carbonate onto the Extruder via Dosing and Continuous Mixing